Autor*innen: Siwara Schmitt, Markus Damm, Jana Heinrich, Florian Balduf.
Kategorie: Smart Manufacturing.
Produktionslinien werden heutzutage für die Herstellung eines Produkts manuell und statisch konfiguriert. Dabei sind bestimmte Produktionsassets in der Regel nur für eine Produktionslinie verfügbar. Deren Rekonfigurationen sind aufwendig und erfordern den Stillstand der Produktionslinie. Allgemein sind unter Produktionsassets jegliche Ressourcen zu verstehen, die zur Herstellung eines Produkts benötigt werden. In diesem Blogartikel sind es im engeren Sinne Maschinen und Geräte.
Durch eine dynamische Rekonfiguration der Produktionsassets zur Laufzeit können diese effizienter und vielfältiger eingesetzt werden. Im Zusammenspiel mit flexiblen Transportsystemen wie Automated Guided Vehicles (AGV), Autonomous Mobile Robots (AMR) oder Autonomous Forklifts entsteht so ein hochflexibler Shopfloor, der den variablen Einsatz von Produktionsassets erlaubt. So lassen sich die Produktionsassets auf virtuelle Produktionslinien planen, die nicht mehr aus einer statischen Anordnung von Produktionsassets bestehen, sondern diese mit anderen virtuellen Produktionslinien teilen. Neue virtuelle Produktionslinien können somit bei vorhandener Kapazität in kürzester Zeit hinzugefügt werden.
Dieser Ansatz eröffnet neue Optimierungspotenziale, die über die Maximierung der Produktionsmengen hinausgehen. So könnte etwa auf zeitlich variable Energiepreise durch die Verschiebung energieintensiver Produktionsschritte in preislich günstigere Zeitfenster reagiert werden. Durch ein intelligentes Scheduling der Produktion können des Weiteren auch Lastspitzen über alle virtuellen Produktionslinien hinweg vermieden werden. Da Produktionsassets austauschbar werden, kann deren Wartung unabhängiger von der Produktion geplant und etwa auf ihre Lebensdauer optimiert werden.
Solch eine rekonfigurierbare Produktion durch virtuelle Produktionslinien ermöglicht hochdynamische Geschäftsmodelle, die folgende Vorteile mit sind bringen:
- Überschüssige Produktionskapazitäten können am Markt angeboten werden
- Statt Produktionsassets zu kaufen, können diese geleast und pro Nutzung abgerechnet werden
- Aufträge können mittels Smart Contracts automatisch abgewickelt werden, die etwa auch Lagerstände berücksichtigen
- Produktionsqualitätseigenschaften und Einsatzstrategien können kontinuierlich evaluiert und simuliert werden
Wie die dynamische Rekonfiguration der Produktion mittels dynamischer Systems-of-Systems umgesetzt werden kann, wird im Folgenden als Beispielsystem dargestellt. Der Begriff System-of-Systems (SoS) wird hierbei nach Gorod et al. (2008) definiert:
»Ein System von Systemen führt eine Reihe von Systemen zusammen, um eine Aufgabe zu erfüllen, die keines der Systeme allein bewältigen kann, wobei jedes konstituierende System sein eigenes Management, seine eigenen Ziele und seine eigenen Ressourcen behält, während es sich innerhalb des SoS koordiniert und sich anpasst, um die Ziele des SoS zu erreichen.«
Im Weiteren wird das Beispielsystem sowie die dazugehörige Architektur vorgestellt, aus der exemplarisch Forschungsfragen für dynamische SoS abgeleitet werden. Darauf folgen die Prozesse, eine Zusammenfassung sowie ein Ausblick zu diesem Thema.
Beispielsystem zur dynamisch rekonfigurierbaren Produktion
Zur Veranschaulichung der Vision wird im Folgenden das Prinzip der Matrixproduktion erläutert (siehe Abbildung 1). Hierbei sind einzelne Produktionszellen wie ein Matrixmuster angeordnet. Produktionszellen sind unabhängige Einheiten mit den verschiedensten Fähigkeiten, wie beispielsweise 3D-Druck, Fräsen oder Montage. Diese einzelnen Produktionszellen sind örtlich unabhängig und über dynamische Transportmittel, beispielsweise rekonfigurierbare Fließbänder, Automated Guided Vehicles (AGVs) oder einen Kran, verbunden. Durch diese dynamische Vernetzung und Rekonfigurierbarkeit wird eine virtuelle Produktionslinie ermöglicht. Abbildung 1 zeigt dazu einen möglichen Durchlauf dieser Matrixproduktion.
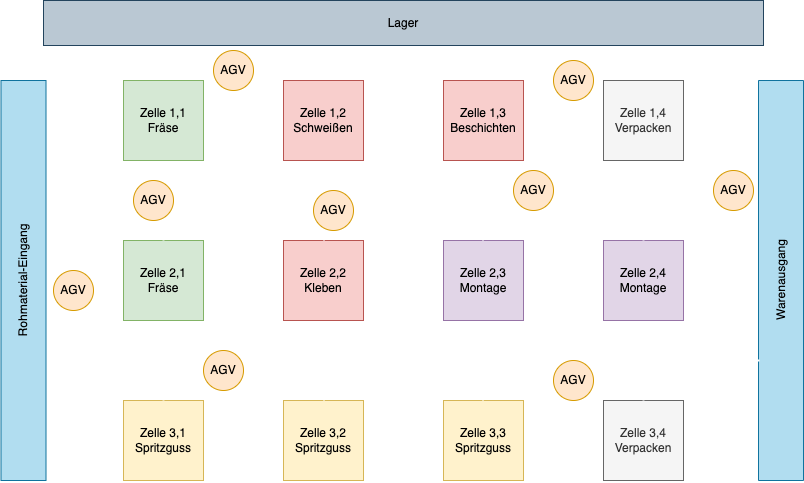
Unsere These ist, dass Innovation in einem Produktionsumfeld hauptsächlich durch Software getrieben wird. Hierzu wird das Beispiel des Produktionsprozess-Sequencings im Kontext der Angebotserstellung betrachtet. In Hinblick auf den Aspekt der dynamischen Allokation von Produktionsassets für die Angebotserstellung lässt sich das Produktionsprozess-Sequencing in mehrere Abstufungen unterteilen. Im einfachsten Fall werden Aufträge direkt einem oder mehreren Arten von Produktionszellen zugeordnet. Hierbei wird ein Rezept oder Produktionsprogramm bereitgestellt und das Enterprise Resource Planning (ERP) berechnet das Angebot. Das Manufacturing Execution System (MES) mappt die Aufträge entsprechend einem übergeordneten Produktionsschedulding auf entsprechende Produktionszellen und organisiert die Intralogistik. Komplexer wird es, wenn ein Auftrag nur mit der Beschreibung des Produkts eingeht, beispielsweise 3D-Pläne oder Materialvorgaben. Dann prüft das ERP-System, ob die Produktionszellen ausreichende Fähigkeiten bereitstellen, um das Produkt herzustellen. Ist dies der Fall, wird ein Rezept für die einzelnen Produktionsschritte sequenziert und ein Angebot erstellt. Dies ist ein Beispiel dafür, wie sich allein über eine Software für das Produktionsprozess-Sequencing die Angebotserstellung und die Produktionsplanung flexibler und effizienter gestalten lassen.
Szenarien wie die soeben beschriebene Angebotserstellung helfen dabei, eine Softwarearchitektur für unser Beispielsystem zu finden. Organisiert als sogenannte Architekturtreiber, bilden sie praktisch Stützstellen für die Architekturerstellung. Abbildung 2 zeigt das oben erwähnte Beispiel des Produktionsprozess-Sequencings als Architekturtreiber.
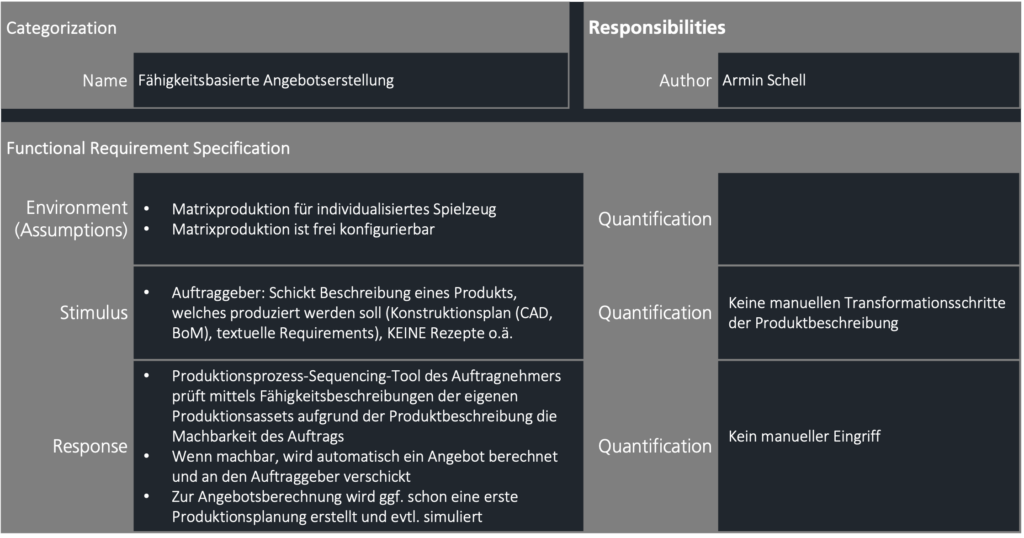
Aus dem obigen Architekturtreiber folgt etwa, dass es in der Architektur eine Komponente zur Erstellung von Rezepten geben muss, die mit der Angebotsberechnung kommuniziert. Diese wiederum kann eine Simulationsengine verwenden. Jeder Architekturtreiber gibt somit Anlass zu einer »Teil-Architektur«, die sich schließlich wie Puzzleteile zu einer Gesamtarchitektur fügen.
Architektur
In unserem Beispielsystem haben sich diese Überlegungen in der Architektur so niedergeschlagen, dass jeder Datenzugriff über Verwaltungsschalen und deren Teilmodelle läuft (siehe Abbildung 3). Es gibt vier Arten von Verwaltungsschalen:
- Jedes Produkt hat eine Verwaltungsschale mit Teilmodellen für Rezepte, Produktionsprozesse und Konstruktionsdaten.
- Transportmittel haben eine Verwaltungsschale mit Teilmodellen für Fähigkeitsbeschreibungen, Simulationen und zur Ansteuerung. Über ein Positionsteilmodell stellen Transportmittel ihre aktuellen Ortsinformationen bereit.
- Jede Produktionszelle besitzt, wie jedes Transportmittel, eine Verwaltungsschale mit Teilmodellen für Fähigkeitsbeschreibungen, Simulationen und zur Ansteuerung. Erweitert werden diese noch um ein Produktionsdaten-Teilmodell zur Bereitstellung aktueller und vergangener Produktionsdaten (letzteres unterstützt durch eine Datenbank).
- Die Fabrik selbst hat eine Verwaltungsschale mit einem aus den Einzelfähigkeiten der Produktionszellen und Transportmittel akkumulierten globalen Fähigkeitenmodell sowie einem Live-Umweltmodell, welches die aktuellen Ortsinformationen von statischen und dynamischen Produktionsassets sowie von Personen, wie bspw. Werker*innen, enthält.
Diese Teilmodelle werden von verschiedenen MES-Prozessen verwendet. So kann etwa der MES-Prozess »Rezepterstellung und Produktionsplanung« aus dem Rezeptteilmodell einen Produktionsprozess generieren, der dann im Produktionsprozessteilmodell abgelegt wird und dadurch späteren MES-Prozessen, insbesondere der Auftragsdurchführung, zur Verfügung steht. Die Auftragsdurchführung wiederum steuert dann auf Basis des Produktionsprozesses die Produktionszellen über deren jeweilige Ansteuerungsteilmodelle an. Auch ERP-Prozesse greifen auf die Teilmodelle zu, bspw. zur Ablage von durch Kund*innen bereitgestellten Rezepten im Rahmen der Auftragsabwicklung oder um für die Planung der Wartung auf Produktionsdaten von Produktionszellen zuzugreifen.
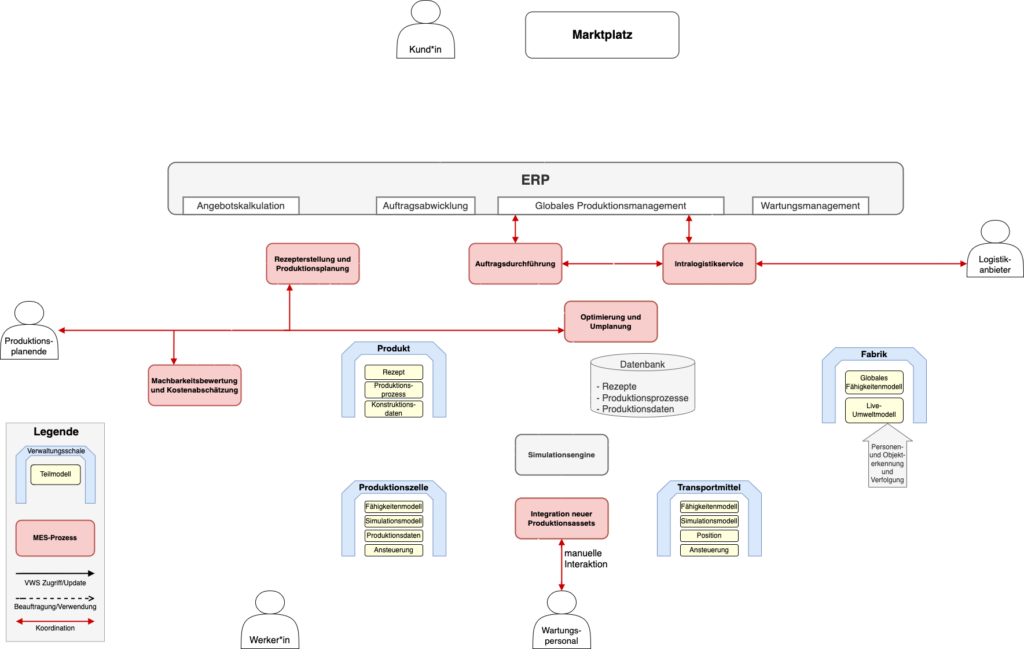
Die Teilmodellzugriffe machen das Gros der Verbindungen in unserer Architektur aus. Die anderen Verbindungen betreffen die Koordination zwischen Prozessen (z. B. zwischen dem MES-Prozess zur Auftragsdurchführung und dem Intralogistikservice), das Anstoßen von Prozessen durch Events (z. B. wenn die globale Produktionsplanung eine Umplanung anstößt, etwa bedingt durch einen Produktionszellenausfall) und menschliche Interaktion, z. B. für nicht-automatisierte Vorgänge in der Produktionsplanung.
Neben den dargestellten MES-Prozessen spielt auch die Simulationsengine eine zentrale Rolle. Sie kann von verschiedenen MES-Prozessen genutzt werden, etwa für die Kostenabschätzung der Produktion eines neuen Produkts oder zum Validieren verschiedener Optionen bei der Umplanung einer Produktion.
Prozesse
Angelehnt an die vorgestellte Architektur lassen sich verschiedene Prozesse der Matrixproduktion ableiten, teilweise als Verfeinerung oder Verallgemeinerung der Szenarien aus den Architekturtreibern. Zur Auftragsabwicklung wird beispielsweise entsprechend einer Angebotsanfrage ein Angebot erstellt. Hierzu schickt ein*e Kund*in eine Produktbeschreibung und weitere Auftragseckdaten, wie z. B. Stückzahl und Lieferzeitpunkt, in Form einer Anfrage bzgl. der Fertigung eines Produkts an die Auftragsabwicklung. Die Anfrage wird anschließend zur Angebotskalkulation weitergeleitet. Die Angebotskalkulation erzeugt eine MES-Instanz für die Machbarkeitsbewertung und Kostenabschätzung und übergibt dieser die Produktbeschreibung und die beabsichtigte Stückzahl. Die MES-Instanz nutzt die Fähigkeitenmodelle der verfügbaren Produktionszellen (auffindbar über deren Verwaltungsschalen) zur Auswahl der verwendeten Zellen und lässt sich von der Rezepterstellung und der Produktionsplanung die entsprechenden Rezepte bzw. Produktionsprozesse sequenzieren.
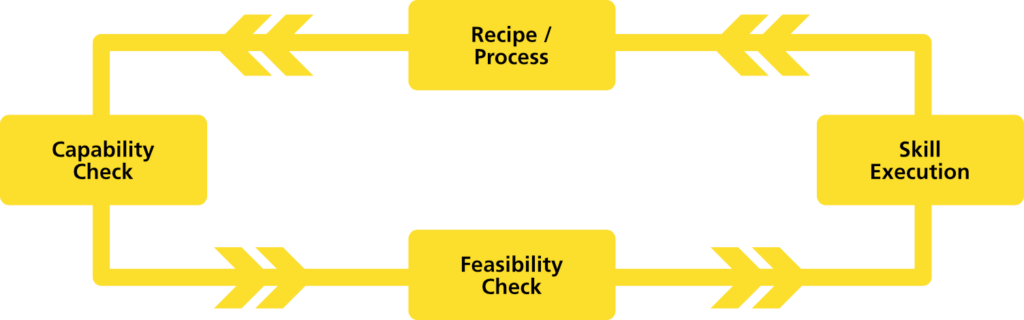
(eigene Darstellung in Anlehnung an Bayha et al. (2020))
Als nächstes folgt das fähigkeitsbasierte Engineering, das in Abbildung 4 veranschaulicht ist. Auf der Basis des Rezepts, das den Startpunkt des fähigkeitsbasierten Engineerings darstellt, wird zunächst überprüft, ob die bestehenden Produktionsassets die Umsetzung des Auftrags grundsätzlich erlauben und ob alle benötigten Fähigkeiten in der Matrixproduktion existieren (Capability-Check). Als Ergebnis dieser Überprüfung werden eine, mehrere oder keine potenziellen Produktionsprozesse identifiziert. Wurde beim Capability-Check mindestens ein Ergebnis identifiziert, wird anschließend ein Feasibility-Check durchgeführt. Dieser überprüft die Umsetzbarkeit der Produktionsprozesse mit aktueller Maschinenauslastung und anderen bestehenden Rahmenbedingungen. Mithilfe einer Simulationsengine können dazu virtuelle Abbildungen der Produktionszellen konfiguriert und angesteuert werden, um so die Produktion des angefragten Produkts zu simulieren. Die Simulationsmodelle der Produktionszellen und Transportmittel sind ebenfalls über deren Verwaltungsschalen abrufbar. Aus der Simulation wird eine Kosten- und Zeitabschätzung erzeugt, welche anschließend wieder an die Angebotskalkulation zurückgegeben wird. Aufgrund der übergebenen Daten wird hier das Angebot erstellt und an den bzw. die Kund*in übermittelt. Die für die Simulation erzeugten Artefakte (wie Rezepte, Fertigungsvorschriften und Produktionsprozesse) werden in der Verwaltungsschale des Produkts gespeichert, um bei der späteren Fertigung wiederverwendet zu werden. Für Tätigkeiten, die nicht automatisierbar sind, ist eine menschliche Interaktion mit der MES-Instanz durch Produktionsplanende notwendig.
Der beschriebene Prozess war lediglich ein exemplarischer Prozess unseres Beispielsystems. Weitere Prozesse sollen in fortführenden Veröffentlichungen detailliert vorgestellt werden. Zu diesen Prozessen gehört zum einen das dynamische Dienstleistungsangebot, welches das Angebot und den Einkauf von Fertigungskapazitäten auf einem externen Marktplatz und den automatischen Umgang mit Änderungen des Auftragsumfangs einschließt. Im Rahmen der Produktion werden die fähigkeitsbasierte Produktionsplanung, die automatische Ausfallkompensierung von Produktionsassets und die Intra- und Extralogistik beschrieben. Da es in der Produktionslinie dynamische Änderungen geben wird, muss darüber hinaus die dynamische Erweiterung von Fähigkeitenmodellen und die automatische Inbetriebnahme neuer Produktionsassets adressiert werden. Um eine fähigkeitsbasierte Produktionsplanung zu ermöglichen, müssen ebenso Machbarkeitsüberprüfungen wie der Capability-Check und der Feasability-Check durchgeführt werden und es muss eine kontinuierliche Optimierung der globalen Produktionsplanung angestoßen und beschrieben werden.
Fazit
In dem skizzierten Beispielsystem der dynamisch rekonfigurierbaren Produktion mittels virtueller Produktionslinien wird vor allem der Aspekt der dynamischen Adaptivität von SoS im Kontext von Smart Manufacturing deutlich. Dieser wird sowohl mit dem fähigkeitsbasierten Ansatz zur Produktionsplanung als auch mit dem fraktalen MES adressiert. Das Potenzial von Fähigkeitsbeschreibungen als einem Teil der Selbstbeschreibung von Systemen ist hier klar erkennbar. Denn mittels der funktionalen Abstraktion von Fähigkeitsbeschreibungen lassen sich Systeme herstellerunabhängig miteinander vergleichen und orchestrieren. Damit können sich SoS zukünftig (teil-)automatisiert und dynamisch an ihre Zielvorgaben anpassen. Die Zuverlässigkeit eines SoS wird durch Feasibility-Checks sichergestellt, die potenzielle Lösungen auf ihre Realisierung hin validieren. Die standardisierte Kommunikation innerhalb eines SoS-Verbundes wird durch das Konzept der Verwaltungsschale und der dazugehörigen Referenzimplementierungen mit Eclipse BaSyx umgesetzt.
Das Beispielsystem zeigt aber auch den Forschungsbedarf zur Umsetzung dieser Vision auf, denn vieles in den beschriebenen Prozessen ist so heute noch nicht umsetzbar. Dies betrifft etwa die Automatisierung der Produktionsplanung und der Rezepterstellung. Eine vollautomatische Erstellung von Rezepten und Produktionsabläufen allein aus Produktbeschreibungen bzw. Konstruktionsplänen von Kund*innen würde eine maximal flexible und dynamische Fertigung ermöglichen. Inwieweit sich eine solche Planungsautomatisierung allgemein auf beliebige Kombinationen von diversen Fertigungsverfahren ausdehnen lässt, ist offen. Auch das Anbieten freier Produktionskapazitäten mit einem Fähigkeitenportfolio ist noch Zukunftsmusik, so wie sich generell die Umsetzung fähigkeitsbasierter Konzepte in der Praxis noch in den Anfängen befindet.
Im weiteren Verlauf der Studie DynaSoS wird das vorgestellte Beispielsystem weiterentwickelt, um somit weitere Forschungsfragen zu identifizieren. Auf einzelne Aspekte des Beispielsystems wird in gesonderten Blogartikeln sowie Veröffentlichungen eingegangen.
Referenzen
Bayha, A., Bock, J., Boss, B., Diedrich, C., & Malakuti, S. (2020). Describing capabilities of Industrie 4.0 components. Whitepaper. Berlin: German Federal Ministry for Economic Affairs and Energy (BMWi), Plattform Industrie 4.0. [Online]. Verfügbar: https:// www.plattform-i40.de/IP/Redaktion/DE/Downloads/Publikation/Capabilities_Industrie40_Components.pdf?__blob=publicationFile&v=3, abgerufen am 22.06.2022
Gorod, A., Sauser, B., & Boardman, J. (2008). System-of-systems engineering management: A review of modern history and a path forward. IEEE Systems Journal, 2(4), 484-499. DOI: 10.1109/JSYST.2008.2007163
Titelbild: © iStock.com/gorodenkoff